‘여객·화물을 넘어 항공기 정비·제작·설계를 병행하는 세계 유일 종합 항공사’
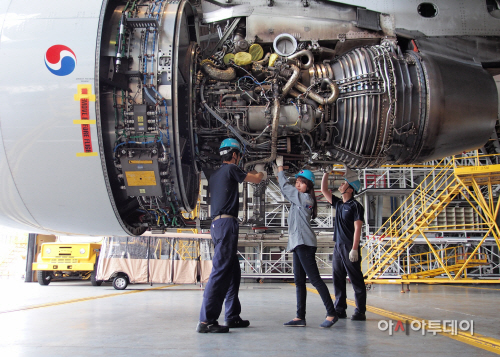 | 20150707 테크센터 취재기념 (5) | 0 | 7일 부산 대한항공 항공우주사업본부 테크센터 내 항공기중정비공장 직원들의 모습./제공=대한항공 |
|
지난 7일 김해국제공항 입구에서 10여분간 차를 타고 달려 도착한 부산 대한항공 항공우주사업본부 테크센터. 약 70만㎡(21만평) 규모를 자랑하는 이곳엔 여기저기 안전을 강조하는 플래카드가 걸려있었다. 각 공장의 직원 2720명은 부슬비가 내리는 여유로운 바깥 환경과는 대조적으로 일사불란하게 움직이고 있었다. 2020년 3조원 매출을 목표로 하고 있는 대한항공 항공우주사업본부의 첫 인상이었다.
◇ 민항기 제조공장 뒤덮은 ‘미래의 먹거리’ 탄소섬유복합재
안내를 받아 보잉·에어버스 등 민항기 제조공장을 방문했다. 안전·청결을 위해 슬리퍼로 갈아신고 들어간 장소는 보잉(B)787 부품 제작공장이었다. 대한항공은 2005년부터 미국 보잉사와 민항기 국제공동개발 사업을 2007년까지 진행했으며 2008년부터는 본격적으로 제품을 생산하고 있다.
이곳에 도착해서야 ‘미래의 먹거리’로 불리는 탄소섬유 복합재를 눈으로 확인할 수 있었다.
초경량 복합소재로 만든 부품은 같은 부피의 알루미늄 무게 10~20%에 해당해 한 손으로도 거뜬히 들 수 있을 만큼 가벼웠다. 탄소섬유복합소재는 가벼울 뿐 아니라 알루미늄과 달리 부식도 되지 않아 2000년대 이후 개발·개량되는 항공기는 대부분 탄소복합재를 사용하고 있다. 기존 항공기는 대부분 무거운 알루미늄을 사용해 속도 등 효율성이 떨어질 뿐 아니라 정비할 때 부식된 부분을 떼내기 위해 재도색해야 하는 단점이 있었다.
대한항공은 B787의 경우 후방 동체·날개끝 등 6가지 부품 가운데 전방동체 하부 부품이자 메탈로 만드는 ‘노즈 휠 웰’을 제외하곤 대부분 복합소재를 사용해 만든다. 최근 대한항공이 50대를 도입하기로 한 B737 맥스(MAX) 시리즈의 날개끝 구조물인 윙렛에도 탄소섬유복합재를 활용한다.
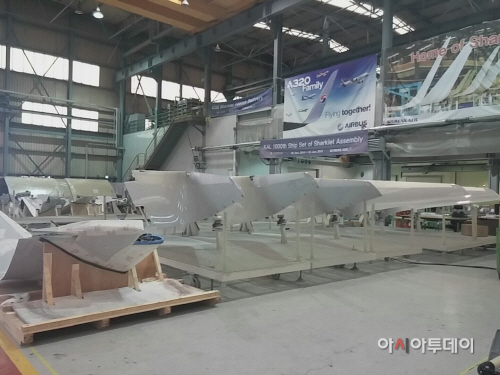 | KakaoTalk_20150709_141406148 | 0 | A320 시리즈에 공급되는 날개끝 구조물 샤크렛이 최종공정을 거치고 있다./사진=문누리 기자 |
|
‘B737 MAX’와 더불어 50대를 도입하기로 결정한 에어버스(A)320시리즈의 날개끝 구조물인 샤크렛에도 복합소재가 사용된다. A350에 장착되는 화물칸 문(카고도어)도 대한항공이 직접 개발해 복합소재로 만들어낸다. 다만 카고도어 아래쪽 등 일부분은 강철과 알루미늄 등도 사용한다. 대한항공은 현재 월 5대의 카고도어를 생산하는데 하반기부턴 월 7대, 내년말 월 10대 생산을 목표로 하고 있다.
이재춘 대한항공 항공우주사업본부 사업계획팀장은 “대한항공 항공우주사업의 효자품목 중 하나가 바로 샤크렛”이라고 말했다. 다만 탄소섬유복합재는 원재료 가공·부품완성 등에 필요한 시설·장비 투자비용이 일반 금속재보다 많이 소요되며 인증 비용도 막대해 기술개발 등 맞춤형 산업 지원 정책이 필요하다는 것이 이 팀장의 설명이다.
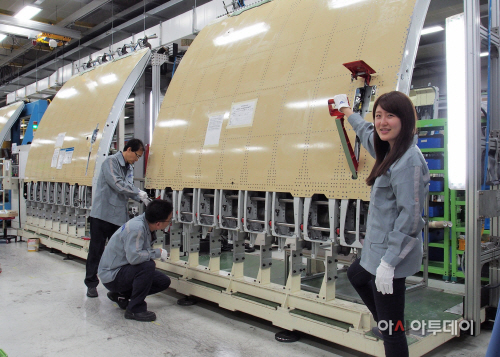 | 20150707 테크센터 취재기념 (2) | 0 | A350에 장착되는 카고도어는 빨간 레버를 내리면 열리는 구조다./제공=대한항공 |
|
◇ “사람으로 따지면 내시경 받는셈”…110명 교대근무로 1~4대 정비
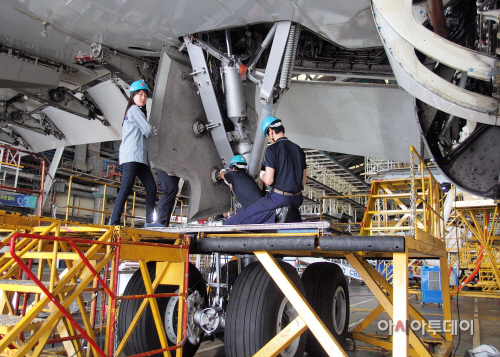 | 20150707 테크센터 취재기념 (3) | 0 | 항공기중정비공장에서 HL7587의 랜딩기어 서포트 페어링 패널을 들어올리는 모습./제공=대한항공 |
|
중·장거리 노선에 투입되는 A330기종의 HL7587을 정비하는 현장은 할리우드 전쟁영화를 연상케 할 정도로 널찍했다. 직접 정비해 볼 기회를 얻어 항공기 정비검사시 떼냈던 랜딩기어 서포트 페어링 패널(커버)을 4명의 현장직원과 함께 힘껏 들어 올렸다. 이후 스패너와 비슷하게 생긴 ‘나쳇’을 들고 부품을 조여 패널을 고정시켰다.
송원석 항공기중정비공장 부장은 “항공기 한 대당 보통 14일에서 20일정도의 정비기간이 소요되고 이곳에서 총 110명의 직원들이 정비를 맡고 있다”며 “사람으로 치면 내시경부터 엑스레이까지 다 받는 셈”이라고 설명했다. 예방정비는 해당 항공기가 두 가지 기준(24개월이나 1만시간) 중 하나라도 채우면 진행하는 정기검사다.
근처 군용기공장에서는 지난해 7월부터 무인화(OPV)·무장탑재 제조사업에 투입된 500MD 헬기에 대한 마무리공정이 진행중이었다. 이 헬기는 1977년 대한항공이 국내 최초로 항공기 조립생산에 성공했던 기종이다. 이 팀장은 “500MD의 경우 시간이 많이 흘렀는데도 실제 사용가능치의 3분의 1 정도밖에 쓰지 않아 무인기로 개조토록 설득해 수주한 케이스”라고 설명했다. 이같이 대한항공 테크센터는 항공기 제작부터 정비·개조까지 도맡아하고 있었다.
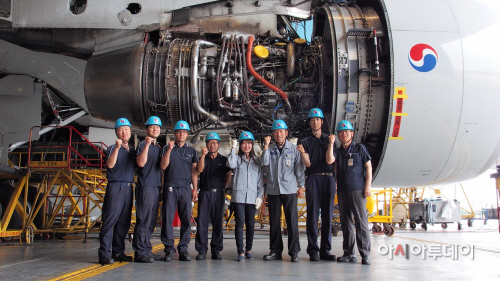 | 20150707 테크센터 취재기념 (6) | 0 | 대한항공 항공기중정비공장을 책임지는 직원들과 기념촬영을 하고 있다./제공=대한항공 |
|